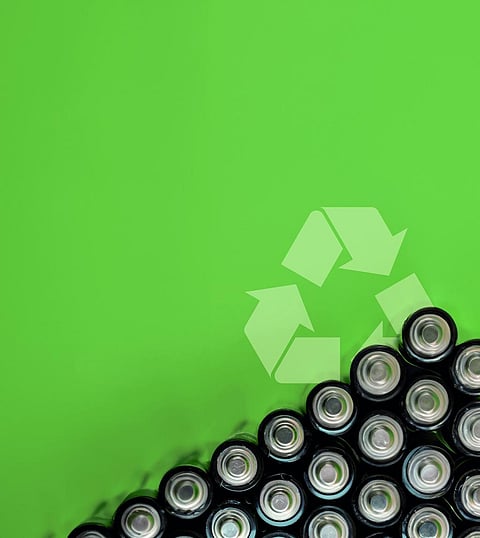
Electric vehicles are key to decarbonise mobility. India’s ambitious electrification programme supported by upscaled domestic battery manufacturing will require a secured supply of battery materials.
But the country does not have enough mineral reserves. At present, its electric vehicle sector is almost entirely dependent on imported battery cells.
Recycling retired batteries can help the sector hedge geopolitical risks, build material security, while minimising environmental hazards from the e-waste and staying on the path to Net Zero emissions. India needs to revamp its Battery Waste Management Rules of 2022 for efficient and economic extraction of the critical minerals through recycling.
Rajat Verma is a new-age scrap merchant. In 2018, he set up a facility in Greater Noida, 30 kilometres south of Delhi, which collects lithium-ion batteries that have reached the end of their useful lives in everything from consumer electronics such as laptop computers and mobile phones to electric vehicles. Engineers and scientists at the facility, Lohum, then carefully dismantle the batteries and extract a variety of valuable materials locked up inside the complex electrical components.
Verma said in 2018, when the facility was set up, consumer electronics used to be a major source of lithium-ion batteries. But since early 2022, they have started receiving a significant volume of electric vehicle batteries. Exigo Recycling at its plant in Panipat, Haryana, has also started receiving lithium-ion batteries from electric vehicles.
In Gurugram, Siddharth Banerji, general manager at Battery Smart, which runs India’s largest network of battery swapping stations for electric two- and three-wheelers, tells Down To Earth (dte) that several electric two- and three-wheelers are beginning to experience quicker deterioration in performance, requiring early battery replacement.
The trickle of spent batteries has started even though India’s electric vehicle market is at a nascent stage — most of the three million electric vehicles in the country have been introduced largely in the past two to three years after the Union government increased consumer subsidy under the second phase of Faster Adoption and Manufacturing of Electric Vehicles in India (FAME-II) in 2021, and their batteries are not expected to have approached end of life.
Though no official data is available to gauge the quantum of electric vehicle batteries that have been retired so far, the volume is expected to explode with India’s rising ambition for electric mobility. Amitabh Kant, India’s G20 Sherpa, during the convenings around the recently concluded G20 Summit, stated that the country plans to achieve 100 per cent electrification of two- and three-wheelers and 65-70 per cent electrification of buses by 2030. India is also one of the 130 signatories to the Zero Emissions Vehicle Declaration made at a side event at the UN Climate Conference (cop26) in Glasgow in 2021. Though not legally binding, signatories to the declaration will ensure that only zero-emission cars and vans are sold by 2040.
Niti Aayog in its 2022 report, Advanced Chemistry Cell Battery Reuse and Recycling Market in India, estimates that the cumulative potential of lithium-ion batteries in India during 2022-30 will be around 600 GWh across all segments in the base case. Of this, 128 GWh will be available for recycling by 2030 with 46 per cent (59 GWh) coming from electric vehicles alone. These retired batteries have enormous potential to power India’s clean energy transition.
Under its “Make in India” initiative, the country aims to become a manufacturing hub for electric vehicles. Companies are already scaling up their operations at home and abroad. However, this ambition is fraught with concerns, particularly around the battery supply chain. Most electric vehicles use lithium-ion batteries because they are energy-dense and offer improved vehicle performance.
These batteries are actually packs of lithium-ion cells that provide electricity. These cells have three essential components: two electrodes (an anode and a cathode) and a medium called electrolyte (that transports ions between these electrodes, thereby generating current). Typically, the anode is made from copper foil with graphite on it, while the cathode is made up of aluminium foil coated with lithium metal oxides (lithium along with other minerals such as cobalt, manganese, iron and nickel, depending on the cell chemistry). The electrolyte is a lithium salt solution such as lithium hexafluorophosphate.
The problem is India does not have reserves of raw materials like lithium, cobalt or nickel to hedge against uncertainties in the battery supply chain. Currently, most of India’s lithium-ion battery requirements are met through imports, especially from China. This makes India’s electric vehicle sector vulnerable to geopolitical turmoil. For instance, the Russia-Ukraine war have brought about uncertainties in the supply chain increasing costs.
Even before the war started, battery metals experienced a fair amount of volatility. Prices of nickel, cobalt and lithium increased by 37 per cent, 41 per cent and 48 per cent, between February 2021 and February 2022, said a policy brief, “Recycling EV Battery Material: Towards material security and sustainability”, by Centre for Science and Environment, Delhi.
For self-reliance in batteries, the industry needs unbridled access to these critical minerals. India is already working towards securing overseas access to lithium mines and global supply chains and is also developing its own new mines. In June this year, it joined the Minerals Security Partnership of the Critical Mineral Club, to catalyse investments from foreign governments and private sector in the critical mineral supply and value chain.
While considerable focus is on sourcing virgin raw material from mines, yet another source of supply that is drawing significant attention globally is reusing the material that is already locked inside the batteries in use and recycling them. Studies have established that these materials can have an infinite life if they can be extracted, separated into battery-grade materials and recycled.
In electric vehicles, a battery is retired once its performance degrades to 70-80 per cent of its original capacity. “These batteries can still be reused for non-automotive applications, such as stationary energy storage,” said Verma. At Lohum, the spent batteries are first inspected for any damage and then tested in the laboratory to assess if they can be reused. Lohum has set up a solar charging station for electric vehicles at its entrance which uses retired batteries.
Those battery packs that do not pass the laboratory testing are dismantled to the cell level. The cells are tested for capacity, internal resistance and other vital electrical properties, which are used to predict the remaining useful life of the cell.
Those found fit for reuse are put into second-life usage such as grid storage; others are sent for recycling. In this phase, the cells are first deep discharged using a salt solution and then passed through a crusher and a shredder after drying.
The resultant material, called black mass, is a mixture of all the valuable materials contained in a lithium-ion cell. The black mass is checked for quality and relevant batches go through extraction, which is essentially a chemical process in which first graphite is recovered, followed by lithium, nickel, cobalt and manganese in that order. These materials can then be used to manufacture anode and cathode and are ready to enter the supply chain again.
The International Council on Clean Transportation, a US-based non-profit, estimates that globally, 1.2 million electric vehicle batteries are expected to reach their end of life in 2030, increasing to 50 million in 2050. Reusing 50 per cent of these batteries and recycling them efficiently can reduce the annual demand for new lithium, cobalt, nickel and manganese mining by 3 per cent in 2030, and 28 per cent in 2050.
There is no denying the fact that retired lithium-ion batteries can help India strengthen its battery material security. But this requires its recycling and refining capacity to increase manifold. Currently, most lithium-ion battery recyclers in the country deal with pre-treatment of spent batteries to extract black mass.
There is little capacity for high-end refining for separation and recovery of battery-grade materials and finally to synthesise cathode material that goes into making a battery. Of the handful of companies involved in recycling of lithium-ion batteries in the country, only seven, such as Exigo, Attero, Rubiman and Lohum, have ultra-refining facilities. That is also because lithium-ion battery recycling is capital intensive.
“Setting up a unit requires an investment of Rs 100-300 crore for end-to-end processing. Every batch of processed black mass and extracted salts needs to be sampled, which is expensive. Testing, grading, and crushing each cell is also a laborious and expensive task,” said Shambhavi Srivastava, business development manager of Reteck Envirotech, an e-waste recycler in Mumbai.
What’s worse is that in the absence of a strong domestic market pull — currently India does not have cell manufacturing capacity and domestic battery manufacturers import cells and assemble them — recyclers face a double jeopardy. They depend on the global market for buying feedstock as well as for selling their final products, which defeats the very purpose of strengthening battery material security through recycling.
Gaurav Dolwani, chief executive officer of Lico Materials, a lithium-ion recycler with a plant in Raigad, Maharashtra, said the country does not have enough battery scrap or black mass to run the plants at full capacity. So recyclers rely on diversified sources of batteries, such as consumer electronics, and on imports, which is a cheaper source. Verma of Lohum claims that his company has a licence to import battery scrap. Most recyclers however prefer importing black mass as the cost of freight for battery scrap is high.
ALN Rao, chief executive officer of Exigo Recycling, said that in a shipment, it is difficult to ascertain whether the batteries are fully discharged and that can add to safety concerns. Battery scrap has to be thus transported in special containers meant for dangerous goods and only a certain kind of vessel can carry them. This makes the freight cost about twice the cost of normal freight.]
On the face of it, importing battery scrap or black mass for recycling appears to help lock in more resources for recovery and reduce the requirements for virgin raw material. However, given the current protectionist trends in the global market, most countries are trying to restrain export of black mass to build their own battery recycling industry. According to the UK-based analytics firm Fast Markets, Europe may stop black mass exports by 2025.
Besides, importing is not going to help India as long as the recycling industry sends the final products to other countries. “The black mass is mostly exported for refining to the global market, where it is priced according to the international price index,” said Srivastava. “Our finished product basically caters to two sets of customers, export customers in the battery industry and domestic customers in non-battery industry,” said Verma. Cobalt, lithium and nickel retrieved through recycling can be used in domestic industries such as steel and paints, he added.
Dolwani of Lico Materials also said that his company is able to extract cobalt sulphate, nickel sulphate or lithium carbonate from recycled batteries. But in the absence of domestic cathode and anode manufacturers, he exports those to China or South Korea. Lico Materials is working with a domestic player, Epsilon Advanced Materials, for manufacturing anode materials. “Once the entire ecosystem is built, it will be possible to keep minerals in India and keep reusing them,” he added.
Several domestic battery manufacturers such as TDSG International, Reliance Industries and Exide are also in the process of setting up cell manufacturing. These companies should be able to produce lithium-ion cells in the next three to four years.
The story first appeared in the print edition of Down To Earth for October 16-31, 2023.