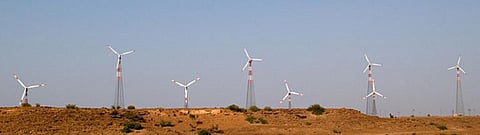
The Indian manufacturers in the wind energy industry have been a forerunner in the development of wind energy sector.
Strong engineering developments helped the industry to reduce capital cost and make itself competitive. They have helped manufacture turbines — stall-regulated and pitch-regulated — of power 250 kilowatt (kW)-2.5 megawatt (MW) and hub heights of 120 meters.
The most recent turbines can harness energy even at slow wind speeds. With a proven track record in technological advancements, India became a popular manufacturing destination. This attracted foreign companies and investors for in-house manufacturing of towers, blades, generators, convertors, etc.
The established model for project development was driven by original equipment manufacturers (OEM). These OEMs bolstered the sector by playing a crucial role in land acquisition, micrositing, data collection and sale of projects.
They also helped with operations and services to small developers on an open-access basis — providing avenues to invest money, signing power purchase agreements (PPAs) at feed-in tariff (FiT) and recovering costs. This helped the sector to self-sustain.
The business model, however, changed with the advent of competitive bidding mechanism. Ideally, this should have expanded the market. However, as ground situations were not thoroughly assessed, it adversely affected the manufacturing sector.
Policy missteps
Auctions are carried out, as part of the bidding mechanism, without a time-table; there is no assurance of a take off.
India's total installed capacity in 2016-17 was 5,500 MW, while manufacturing capacity was 10,000 MW. But auctions fell to 1,500 MW.
The process lacks clarity and auctions are not being announced regularly. This limits growth of the sector.
Auctions are based on unrealistic tariff caps. The rush for cheapest tariffs is creating more problems. Due to intense competition, the independent power producers (IPPs) are likely to bid for large quantities at the lowest possible tariffs and squeeze profit margins of manufacturers.
According to Sunil Jain, chief operating officer, Hero Futures Energy, the industry is forced to reduce capital cost due to reducing tariffs. But the industry has some inventory along with them, which developers force them to provide for minimum cost.
"This makes the producer’s balance sheet weak and financial health poor. Big manufacturers in India are collapsing.”
Failing businesses
Persisting problems such as auction cancellations, PPA renegotiations, payment delays are eroding the trust of investors. The combined effect of these challenges and failing projects are forcing manufacturers to lay-off or shut operations.
Homegrown Suzlon Group, one of the biggest wind sector companies in India, reported a net loss of Rs 778 crore in the second quarter of the year through March 2020 — up by 64 per cent from the same period previous year when the net loss was Rs 280 crore.
The group caters to over 35 per cent of the country’s wind installations and is a custodian of over 12.5 gigawatt (GW) of wind assets (over 8,500 turbines) under service in India.
The company has defaulted on loans, bonds and interest payments and owed Rs 12,785 crore to creditors, as of January 2020.
It is now restructuring its debt to avoid bankruptcy. It may also divest or dilute its investments, assets and undertakings. Suzlon’s market share in total installations dropped to 19 per cent in 2019 from 41 per cent in 2018.
Profits started to decline for manufacturers from 2015-16 onwards, making it difficult for them to survive. This has prompted closure of certain manufacturing facilities. (See table below).
Net profit of wind manufacturers
* Till December. Source: BSE |
“In 2016, we had 10 GW of wind turbine generation manufacturing capacity in India. Till 2016, we had 21-22 manufacturers. But now, only 6-7 are completely operational,” said Manish K Singh, general secretary, Indian Wind Energy Association.
With no non-performing assets (NPA), the wind energy sector has not hit rock bottom so far.
Bankers’ apprehension is that Suzlon’s failure might result in a domino effect. In one of the earliest instances, corporate insolvency resolution process of ReGen Powertech was ordered by the National Company Law Tribunal — quasi-judicial body in India that adjudicates issues relating to Indian companies — in early December 2019.
No incentives for exports
The industry is not supported for exports, despite its state-of-the-art wind energy equipment and potential to become significant part of global supply chain. Indian manufacturers lose competitive edge over freight, logistics costs and high bank rate.
Currently, the industry exports worth $500 million per annum of wind turbine and components. If it is provided incentives, the same can increase four-fold to $2 billion.
But the government has no such plans. “The government has not formulated any special scheme for promoting manufacturing of equipment used in the generation of wind power,” said RK Singh, minister of state for new & renewable energy and power.
Concerted efforts required
Ironically, the wind sector is struggling to survive. Meanwhile, the government is focusing to develop a solar manufacturing industry.
Concerted efforts are needed to revive the industry by eliminating suffocating policies.
A timetable for auctions, with a capacity addition of about 10 GW per annum, would give the industry a much required market. It would also help the industry realise its potential of becoming the manufacturing hub for southeast Asia.
In addition, the capacity for equipment production for offshore installations should be enhanced. The sector could take the centre-stage in many countries, and help India attain its target of adding 30 GW of capacity to the sector.